Metody optymalizacji procesów produkcyjnych
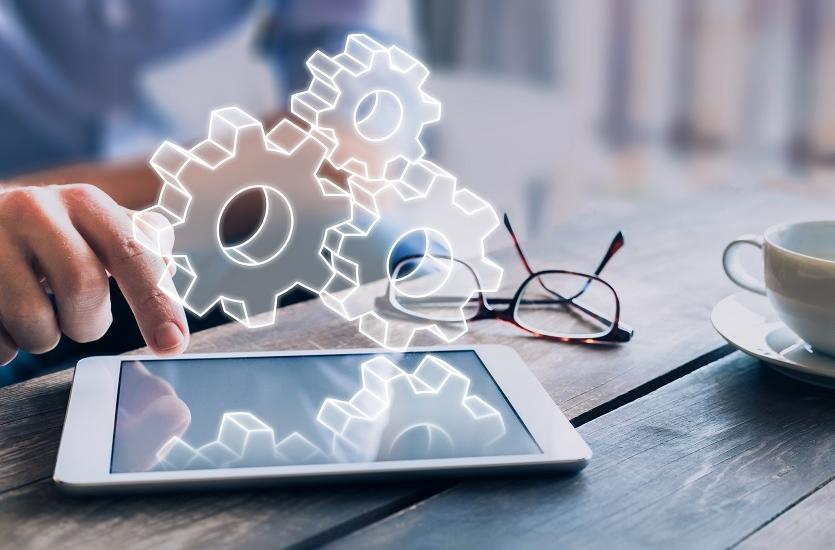
Optymalizacja procesów przemysłowych przeprowadzana jest w warunkach dużej konkurencyjności firm produkcyjnych. Wśród profitów wynikających z jej wprowadzenia można wyróżnić zarówno wzrost zysków, ale i skuteczną reorganizację pracy w przedsiębiorstwie. Praca staje się wówczas efektywniejsza przy jednoczesnym obniżeniu kosztów. Optymalizacja procesów przemysłowych rozpoczyna się wraz z zebraniem informacji, a następnie ich wnikliwą analizą.
Kiedy należy zastosować optymalizację procesów produkcyjnych?
Optymalizacja procesów produkcyjnych jest niezbędna w przypadku, kiedy finalny koszt wytworzenia danego produktu znacznie przewyższa jego sprzedaż. Ponadto warto się na nią zdecydować, gdy procesy produkcyjne zajmują zbyt wiele czasu, a koszty wytworzenia produktu stale wzrastają. Firma dążąca do wypracowania większej konkurencyjności na rynku, czy też pragnąca zadbać o poprawę komunikacji zespołu pracowników powinna wziąć pod uwagę optymalizację, którą fachowo wykonują wyspecjalizowane w tym firmy, takie jak chociażby Redhawk. Jakie metody optymalizacji procesów produkcyjnych warto wymienić?
Metoda mapowania
Grafiki opisujące operacje występujące w procesach przemysłowych oraz powstałe zależności między działami – tak w dużym skrócie wygląda metoda mapowania. Metoda ta uwzględnia również wszystkie procedury oraz odnosi się do zapisów sporządzonych dokumentacji. Mapowanie powinno być przeprowadzone w sposób transparentny, tak aby jak najbardziej oddać istotę procesów przemysłowych danego przedsiębiorstwa. Dodatkowo mapowanie może zastąpić długotrwały i monotonny proces wprowadzania nowych pracowników do firmy.
Metoda Kaizen
Metoda Kaizen, nazywana inaczej metodą małych kroków, służy ku polepszeniu warunków pracy panujących w przedsiębiorstwie. Metoda ta umożliwia poczynanie małych kroków, co sprawia że można błyskawicznie wprowadzić nowe rozwiązania zastępujące te, które nie działają w prawidłowy sposób. Metoda Kaizen opiera się na 10 zasadach: problemy prowadzą do nowych możliwości, 5 pytań "dlaczego?", wszystkie pomysły są równie ważne, wprowadzanie realnych rozwiązań, odrzucanie ustalonego stanu rzeczy, nie wymyślanie zbędnych wymówek, proste i nieidealne rozwiązania są o wiele lepsze od tych pozornie idealnych, spryt jest więcej wart aniżeli pieniądze, konieczne jest korygowanie błędów na bieżąco, ulepszanie to niekończący się proces.
Metoda Kanban
Metoda Kanban powstała w latach 50. w Japonii. Opiera się ona na stworzeniu wizualizacji procesów, które mają zostać wdrożone w przedsiębiorstwie. Optymalizacja procesu pracy ma w konsekwencji doprowadzić do wypracowania systemu produkującego zgodną z zapotrzebowaniem liczbę dóbr. Metoda Kanban opiera się na zasadzie "7 razy żadne": żadne braki, żadne zapasy, żadne opóźnienia, żadne kolejki, żadna bezczynność, żadne zbędne czynności i kontrole, żadne zbędne przemieszczenia. Stosowanie tej metody owocuje zredukowaniem wyrobów gotowych oraz magazynów przedprodukcyjnych.
Metoda 5S
Nazwa tej metody wywodzi się od 5 japońskich słów: SEIRI (porządek: etap eliminacji zbędnych przedmiotów i sposobów produkcji), SEITON (organizacja: zorganizowanie miejsca do składowania narzędzi wykorzystywanych do produkcji), SEISO (sprzątanie: uporządkowanie miejsca pracy), SEIKETSU (utrzymanie czystości: aspekty umożliwiające utrzymywanie porządku w przedsiębiorstwie i organizacja pracy), SHITSUKE (samodyscyplina: przestrzeganie wypracowanych zasad SEIRI, SEITON, SEISO, SEIKETSU). Wprowadzenie metody 5S powinno być poprzedzone szkoleniami dla pracowników, ukierunkowanym na przedstawienie skutecznych sposobów na wprowadzanie w życie 5S.