Charakterystyka i proces produkcji sztucznego metalu
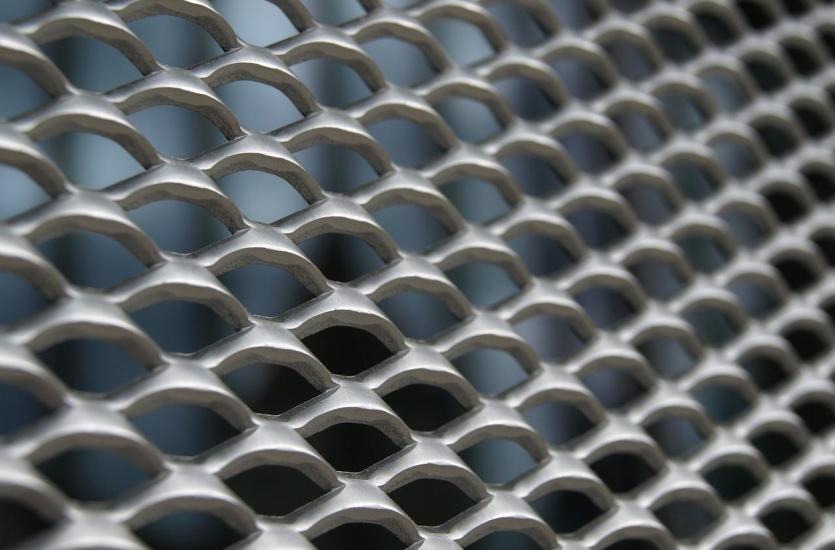
Tworzywa sztuczne są materiałami otrzymywanymi z połączenia polimerów z różnymi, w zależności od konkretnego produktu, dodatkami. Zaliczają się do nich m.in. napełniacze, stabilizatory, zmiękczacze, pigmenty, antystatyki oraz antypiryny. Tworzywa sztuczne są wytworami użytkowymi, stosowanymi m.in. w przemyśle, jednym z otrzymywanych wyrobów jest sztuczny metal.
Charakterystyka sztucznego metalu
Sztuczny metal, jako jeden z wyrobów zaliczających się do tworzyw sztucznych, wyróżnia się przede wszystkim małą gęstością, wysoką wytrzymałością właściwą oraz wysokimi właściwościami elektroizolacyjnymi. Ponadto nieodzowną cechą, istotną dla materiałów z polimerów, jest niewątpliwa odporność na oddziaływanie czynników chemicznych, a także bezproblemowość w tworzeniu różnorakich kształtów, w zależności od wymogów projektu. To bardzo ważne w bardziej skomplikowanych wyrobach, które wymagają precyzji wykonania. Trzeba jeszcze wspomnieć o możliwości otrzymania pożądanego wyglądu wytworów, a najwyższa jakość nie jest oczywiście bez znaczenia. Niestety materiały sztuczne nie są pozbawione wad, ponieważ nie są odporne na oddziaływanie cieplne, promienie UV czy uszkodzenia mechaniczne.
Produkcja sztucznego metalu
Najważniejszy w trakcie produkcji sztucznego metalu i pozostałych tworzyw sztucznych jest czujność i uwaga zespołu zajmujących się realizacją poszczególnych projektów – mówi nasz specjalista z firmy AnbiTech.
Sama produkcja nazywana jest formowaniem i może odbywać się w różnorakich procesach. Pierwszy z nich to proces wtryskiwania materiału do formy, następnie zestaleniu go i utwardzeniu. Drugi proces jest procesem wytłaczania, czyli przepychania uplastycznionego tworzywa przez odpowiedni kanał dyszy wytłaczarskiej. Prasowanie z kolei jest wprowadzaniem konkretnego materiału do formy, która wymaga jeszcze nacisku przez specjalny stempel. Trzeba jeszcze wspomnieć o odlewaniu materiałów, porowaniu, formowaniu podciśnieniowym, nawarstawianiu oraz nanoszeniu. Później konieczne są jeszcze obróbki wykańczające, do których zaliczają się zgrzewanie, spawanie, klejenie, laminowanie, jak również obróbki powierzchniowe czy ulepszające.