W jakich maszynach wykorzystuje się silniki hydrauliczne?
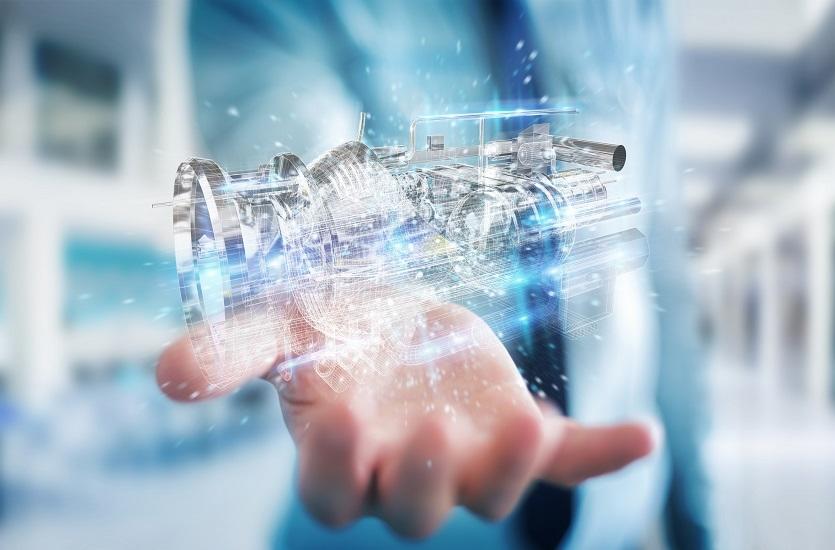
Istnieje wiele sytuacji, w których dostarczenie napędu za pomocą powszechnie stosowanych silników spalinowych lub elektrycznych jest mało efektywne albo niemożliwe z przyczyn konstrukcyjnych czy też z uwagi na warunki, w jakich będzie musiało pracować urządzenia. Rozwiązaniem jest w takiej sytuacji zastosowanie silników hydraulicznych, osiągających znakomite parametry użytkowe – dobrą wydajność połączoną z dużymi możliwościami sterowania.
Jaką funkcję pełnią silniki hydrauliczne i gdzie się je montuje?
Stosowanie hydrauliki siłowej sprawdza się we wszystkich rozwiązaniach, gdzie potrzebne jest przekazanie dużej ilości energii, którą łatwo można zamienić w wysoki moment obrotowy lub zdolność do przeniesienia znacznej masy. Za sprawą wytworzenia odpowiedniego ciśnienia i wymuszenia przepływu cieczy, zwanej czynnikiem hydraulicznym – najczęściej oleju, ale niekiedy także wody czy różnych emulsji wodnych i roztworów – dochodzi do zgromadzenia, a następnie przekazania do odbiornika zmagazynowanej energii potencjalnej. Układ hydrauliczny umożliwiający wykonanie takiej pracy składa się z pompy, zbiornika cieczy hydraulicznej i układu przewodów oraz zaworów, które pozwalają na sterowanie przepływem. Do zmiany energii potencjalnej zgromadzonej w czynniku hydraulicznym konieczny jest również odpowiedni odbiornik – cylinder hydrauliczny zwany też siłownikiem, za pomocą którego można uzyskać ruch posuwisty lub posuwisto-zwrotny, albo silnik hydrauliczny, dzięki któremu można wygenerować ruch obrotowy – wyjaśnia ekspert z firmy HYDRO-DYNA, specjalizującej się w obsłudze urządzeń hydrauliki siłowej.
Silnik hydrauliczny jest w stanie zmienić energię potencjalną zmagazynowaną w cieczy dzięki jej naporowi na elementy robocze. W zależności od konstrukcji silnika może to być powierzchnia tłoków, uzębienia koła zębatego czy też membrany. Silniki hydrauliczne pozwalają na zmianę energii hydraulicznej na ruch obrotowy elementów roboczych silnika lub podobnie jak w przypadku cylindrów hydraulicznych, na ruch posuwisto-zwrotny, który następnie jest już mechanicznie zamieniany na obrotowy, np. za pośrednictwem mimośrodu. Silniki mogą się różnić nie tylko zasadą budowy, ale również stałą lub zmienną chłonnością, czyli swoją pojemnością roboczą decydującą o zakresie prędkości obrotowej, jaką są w stanie wytworzyć. Istnieją zarówno silniki o stałej pojemności, w przypadku których prędkość obrotowa jest uzależniona wyłącznie od parametrów przepływu, jak i takie, gdzie może być ona zmienna, a zatem regulowana mimo stałego przepływu.
Silniki hydrauliczne wykorzystuje się do napędu maszyn i urządzeń, a także ich poszczególnych podzespołów. Do ich podstawowych zalet należą bardzo niska bezwładność układu, która umożliwia szybkie wytworzenie wysokiego momentu obrotowego, ale również zdolność do osiągania szerokiego zakresu prędkości obrotowych – zarówno niewielkich, jak i stosunkowo wysokich, co ułatwia precyzyjny dobór potrzebnych parametrów pracy. Zaletą silników hydraulicznych jest bardzo cicha praca, wysoka niezawodność oraz znacznie niższy poziom wibracji w porównaniu z silnikiem spalinowym. Duże znaczenie ma też fakt, że w przypadku silników hydraulicznych przekazywanie energii niezbędnej do działania nie wymaga skomplikowanych i ciężkich przekładni, co wpływa na obniżenie masy całego urządzenia. Czynnik hydrauliczny może być bez problemu przekazywany za pomocą elastycznych przewodów, co oznacza, że silniki mogą się znajdować na podzespołach połączonych przegubami, ramionami czy wysięgnikami, co przy stosowaniu rozwiązań mechanicznych byłoby znacznie bardziej skomplikowane. Plusem jest fakt, że silniki hydrauliczne mogą zwykle pracować w różnych pozycjach. Ważna jest stosunkowo niewielka masa samego silnika w porównaniu z konstrukcjami spalinowymi czy elektrycznymi. Często liczy się również fakt, że silniki hydrauliczne działają beziskrowo, dzięki czemu można ich używać w atmosferze zagrażającej wybuchem.
Skala zastosowań silników hydraulicznych jest bardzo szeroka. Powszechnie montuje się je w ciężkim sprzęcie budowlanym i rolniczym, a także w urządzeniach wykorzystywanych w przemyśle, zwłaszcza wydobywczym – w kopalniach i na platformach wiertniczych. Dość często są używane jako źródło napędu m.in. w przenośnikach taśmowych, wentylatorach, ślimakach wtryskarek i wytłaczarek do produkcji tworzywa sztucznego czy dużych świdrów.
Rodzaje silników hydraulicznych i zasada ich działania
Silniki hydrauliczne mogą mieć różną konstrukcję, najczęściej można spotkać silniki zębate, łopatkowe oraz tłoczkowe. Jednymi z najczęściej stosowanych są hydrauliczne silniki zębate. Wyróżniają się one bardzo kompaktową budową i prostotą, która gwarantuje niewielką awaryjność oraz wysoką wytrzymałość urządzenia. Zaletą silników hydraulicznych jest fakt, że mogą one działać w obu kierunkach, za sprawą zmiany przepływu czynnika hydraulicznego. Plusem jest możliwość uzyskiwania dużej prędkości obrotowej, natomiast pewnym ograniczeniem bywa to, że mają stałą pojemność roboczą. Silniki wykorzystujące mechanizm zębatkowy mogą pracować przy wysokim ciśnieniu i przypływie, nie są wrażliwe na wyższe temperatury pracy i na rozmaite charakterystyki lepkości czynnika hydraulicznego.
Zasada działania hydraulicznego silnika zębatego opiera się na współpracy dwóch kół zębatych umieszczonych w szczelnej obudowie. W przypadku, gdy oba koła mają uzębienie zewnętrzne, przepływ czynnika wywiera nacisk na powierzchnię zębów, powodując ich obrót. Istnieją również silniki, w których jedno z kół ma uzębienie wewnętrzne, a drugie, pełniące funkcję wirnika uzębienie zewnętrzne. Przepływ cieczy hydraulicznej wymusza ruch wirnika, który porusza się planetarnie. Silniki tego rodzaju są nazywane gerotorowymi. Korzyścią ze stosowania takiego rozwiązania jest możliwość uzyskiwania wysokiego momentu obrotowego przy niedużej prędkości obrotowej.
Silniki łopatkowe pracują za sprawą naporu cieczy na łopatki zamontowane w wirniku. Wirnik porusza się wewnątrz obudowy mimośrodowo, a łopatki są dociskane do wnętrza korpusu za sprawą mechanizmu sprężynowego, co pozwala na zachowanie szczelności układu. Silniki tego rodzaju są dość wrażliwe na jakość czynnika hydraulicznego. Pompy łopatkowe są nieco bardziej złożone pod względem konstrukcyjnym niż zębate, z uwagi na większą ilość elementów ruchomych, jednak ich awaryjność jest niska, a naprawa bądź wymiana wirnika z reguły bardzo prosta.
Silniki tłoczkowe, zwłaszcza w wariantach wielotłoczkowch wyróżniają się bardziej złożoną budową, łączy się ona jednak z możliwością doboru charakterystyki ich pracy oraz wysoką wydajnością. Wykorzystują zasadę, na jakiej działają siłowniki hydrauliczne – ciecz naciska na powierzchnię tłoka, przesuwając go. Dzięki przekładni mechanicznej ruch ten może być przekazany za pośrednictwem mimośrodu lub wychylnej tarczy. Silniki wielotłoczkowe występują w wersjach promieniowych – w takim przypadku ruch obrotowy jest uzyskiwany za sprawą zmian położenia tłoczków, które pracując kolejno, wymuszają obrót, poruszając się po wewnętrznej bieżni lub pozostając w stosunku do niej nieruchome – a także osiowych. W silnikach osiowych ruchy kolejnych tłoków powodują obroty tarczy ustawionej do nich pod kątem. Przy takiej konstrukcji możliwe jest regulowanie wydajności silnika przez zmianę kąta wychylenia tarczy, z którą są połączone tłoczyska poszczególnych tłoków.